Blyth Offshore Wind Farm - Dynamic Monitoring
Challenge
The Blyth Offshore Demonstrator Wind Farm Project involved successful construction of five wind turbines 6.5 km off the Northumberland coast at a water depth of 38 metres. The turbines have a combined generation capacity of 41.5 MW, enough low carbon energy to power 34,000 homes, whilst cutting annual CO2 emissions by 57,600 tonnes.
The ambitious project, delivered by EDF Energy Renewables in 2017, applied a ground-breaking and experimental construction technique. The concrete gravity based foundations (GBFs) - the support structures of the wind turbines - were designed and built by BAM on land and then installed using a “float and submerge” method. The GBFs were towed out to sea then sunk onto the sea floor, providing huge cost savings compared to traditional methods utilising expensive heavy-lift crane vessels.
BAM chose Senceive technology in order to provide a reliable and robust wireless monitoring solution which could be used to confirm the stability of the GBFs during towing and submersion.
Solution
Two FlatMesh™ high precision waterproof triaxial tilt sensor nodes were installed on each of the five GBFs. They were positioned around steel platforms on top of each of the GBF’s steel masts. Senceive’s innovative magnetic mounting system, with pull force of 100 kg, enabled engineers to quickly and securely install the tilt nodes as well as five solar powered gateways – one for each GBF. The BAM team responsible for monitoring the GBFs chose to install the triaxial tilt nodes at a right angle to each other; this provided a degree of redundancy in the unlikely event of sensor failure or disturbance, and enabled corroboration of the readings.
The nodes were set to an initial reporting frequency of 1 minute for the dry dock testing period, increasing to 1 second during towing and submersion. Trigger levels were set to alert stakeholders via SMS text message in the event of movement outside design thresholds.
Data was relayed from the sensors to a gateway on each mast and then wirelessly sent to registered stakeholders who could access the data online using Senceive's WebMonitor visualisation software.
Outcome
BAM was able to demonstrate that the GBFs were as stable throughout the towing and final submersion as the design had predicted.
The innovative float and submerge method proved highly successful, with the only movement shown in the dynamic data being due to tides. The Senceive wireless system was found to be quick and simple to install, as well as robust and reliable in particularly harsh and challenging marine conditions.
Downloads
Created on: Tue 2nd Feb 2021
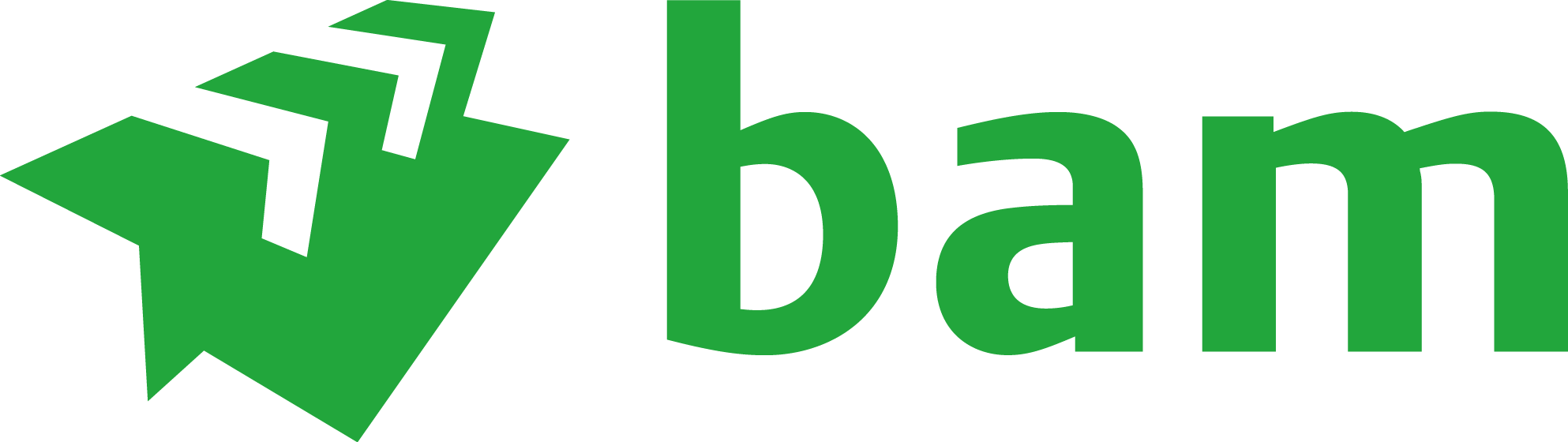
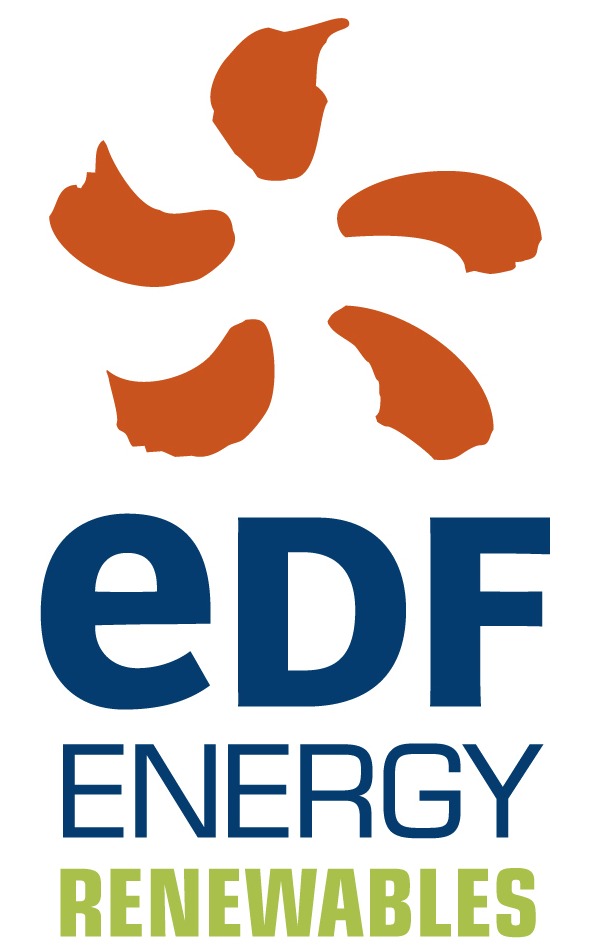
Having Senceive wireless tiltmeters in place gave a very quick and accurate insight into how the GBF responded to every load of ballast that was put in.