Chipping Sodbury Tunnel - Structural Monitoring
Challenge
Chipping Sodbury Tunnel, near Bristol, was completed in 1902. The twin track masonry structure is 4,000 m long and is the second longest tunnel on the Western Route linking London and South Wales.
Network Rail has been implementing an extensive programme of improvements to the route since 2010 which includes installing overhead electrification.
In order to accommodate the overhead line equipment (OLE), there was a need to modify many structures, including Chipping Sodbury Tunnel. Works included lowering the track by 150 mm and improving the track drainage.
In the Autumn of 2020, AECOM engineers undertook a structural assessment to evaluate the potential impact of the track lowering works on both the tunnel and the central track drainage culvert. This assessment informed the implementation of a remote tunnel monitoring regime which was required to provide the necessary assurance that the works could be undertaken safely.
The monitoring scheme aimed to verify the findings of the structural assessment and inform decision making, particularly in the event of measurements exceeding predicted values.
The monitoring design was guided by principles outlined in the British Tunnelling Society publication, ‘Monitoring Underground Construction - A Best Practice Guide’, alongside the Network Rail standard NR/L2/CIV/177 – ‘Monitoring track over or adjacent to Construction Works’.
Monitoring design and arrangements also drew on experiences gained by AECOM on similar track lowering projects where structural monitoring was also required. This included several locations of the Great Western Railway Modernisation Scheme, namely; Patchway Tunnels, Box Tunnel, Middle Hill Tunnel, Dundas Aqueduct, Sydney Gardens, and Alderton Tunnel.
Devising a rail monitoring solution for Chipping Sodbury was not straightforward. Factors to consider included: the need to maintain continuous operation and data transfer from the system at distances greater than 2 km from access points; the need to avoid interference with the construction works and to avoid damage to the system arising from the works, and the need to maintain reliable monitoring performance in conditions that were, at times dusty, waterlogged and prone to significant vibration.
Solution
AECOM chose Senceive’s FlatMesh™ Nano triaxial tilt sensor nodes as the primary technology for monitoring the tunnel lining. This was largely due to the associated operational advantages, including their compact size, robust construction and better performance in the wet tunnel environment compared to conventional tilt sensors.
Over 200 Nano tilt sensors were installed on the tunnel lining to provide a flexible and high-resolution monitoring system able to capture the limited movements anticipated. The main limitation was that the sensors would measure relative, rather than absolute movements. Whilst this was sufficient to identify and quantify the anticipated modes of movement, a decision was made to provide supplementary monitoring to verify that the system and structure were performing as expected. This used tilt nodes mounted on beams.
Wireless tilt chains – Nano tilt sensors mounted onto aluminium beams - offered an alternative to Shape Accel Arrays (SAAs); however, a review of gauging clearances showed that it would not be possible to install them around the full tunnel profile due to localised pinch points. Nevertheless, shortened tilt chains were installed in high risk areas where they could be safely accommodated.
To further enhance performance, a number of Optical Displacement Sensors (ODS) were installed as a secondary means of monitoring at selected locations. The ODS nodes provided a different type of measurement (based on laser distance measurement as opposed to MEMS sensor) and were therefore considered to be a useful tool for verifying overall tunnel deformations. The ODS nodes were positioned in three modes: on opposing sidewalls; on the haunches pointing at the sleepers, and at the crown.
The ODS nodes directed at the track were susceptible to interference from construction activity. The monitoring team therefore selectively paused ODS alerts when construction activity that interfered with line of sight was taking place in their immediate proximity in order to prevent false alerts being triggered.
In addition to monitoring the tunnel lining, track monitoring was also conducted. This used a total of 834 Senceive High-G Triaxial Tilt Sensor Nodes at 3 metre intervals throughout the main works area and 30 m beyond the zone of influence. Relative and absolute twist and cant were monitored. The absolute cant was calculated using surveyed cant readings, which was then used as a constant offset to the incoming data from these tilt sensors.
There was a further need to check the behaviour of the central track drain culvert, but access considerations prevented mounting instruments directly on the buried structure. A decision was made to monitor the track above to identify any deformation that could indicate failure of the drain. This was achieved using High-G Triaxial Tilt sensor nodes installed at 6 m intervals outside the main works area.
Power for the gateways was not available via the usual options of solar panels or mains supply. This was solved by using 12v 110Ah batteries connected to a 12vdc to 24vdc converter. With periodic charging of the batteries this provided a reliable means of continuously powering the system and relaying data onwards to the WebMonitor data viewing platform. The system was configured to send automated alerts warning of any movement that exceeded pre-selected threshold values.
Outcome
The effectiveness of the monitoring programme at this challenging site was built on a combination of the expertise of AECOM’s structural and monitoring engineers and the ease of deployment and reliability of the Senceive technology.
The use of Nano and ODS sensors on the tunnel lining allowed the anticipated movements of the lower side walls to be monitored without interfering with the works. This was a key consideration given the restricted programme of works (the tunnel closure was only three days) and the nature of the construction works which restricted access and line-of-sight.
An extended programme of monitoring was needed to verify the behaviour of the culvert due to the changes in loading following the track lowering. As a result, monitoring was installed post-works on the down line track. Over 400 sensors were installed on the trackbed by two engineers within just four hours. Once movement was shown to be stable, the sensors were removed, with the rest of the monitoring equipment removed in the following weeks.
The sensors will likely be re-deployed on a future AECOM project.
Downloads
Created on: Tue 6th Apr 2021
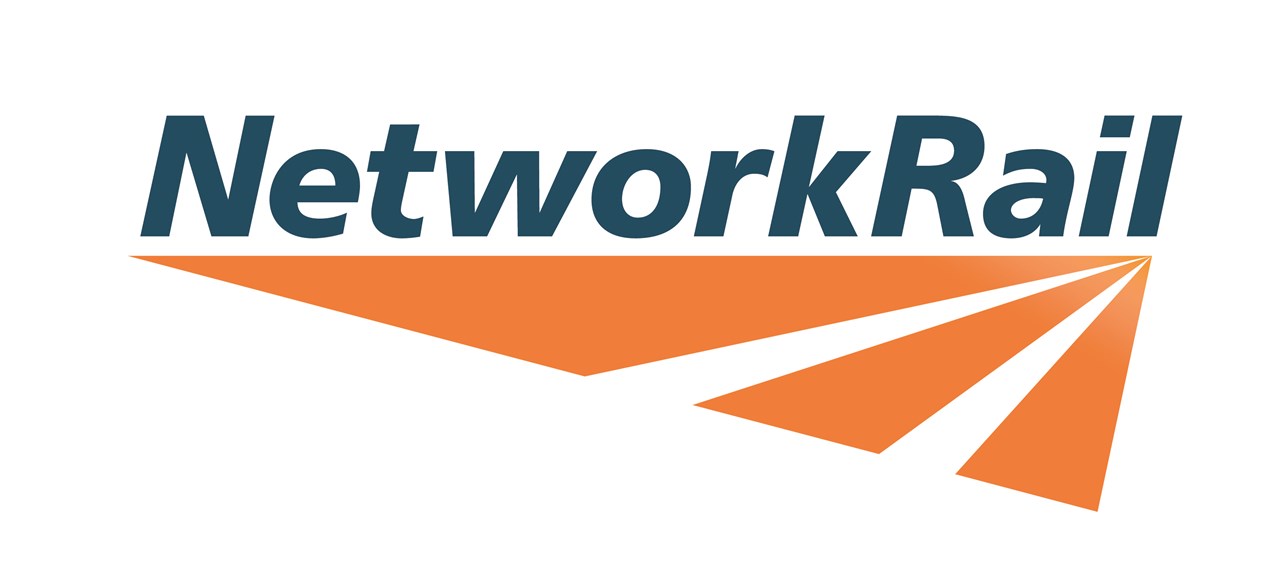
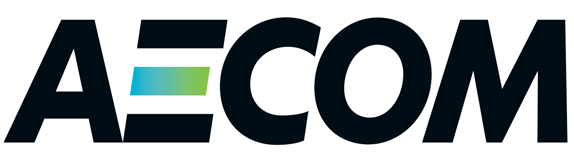
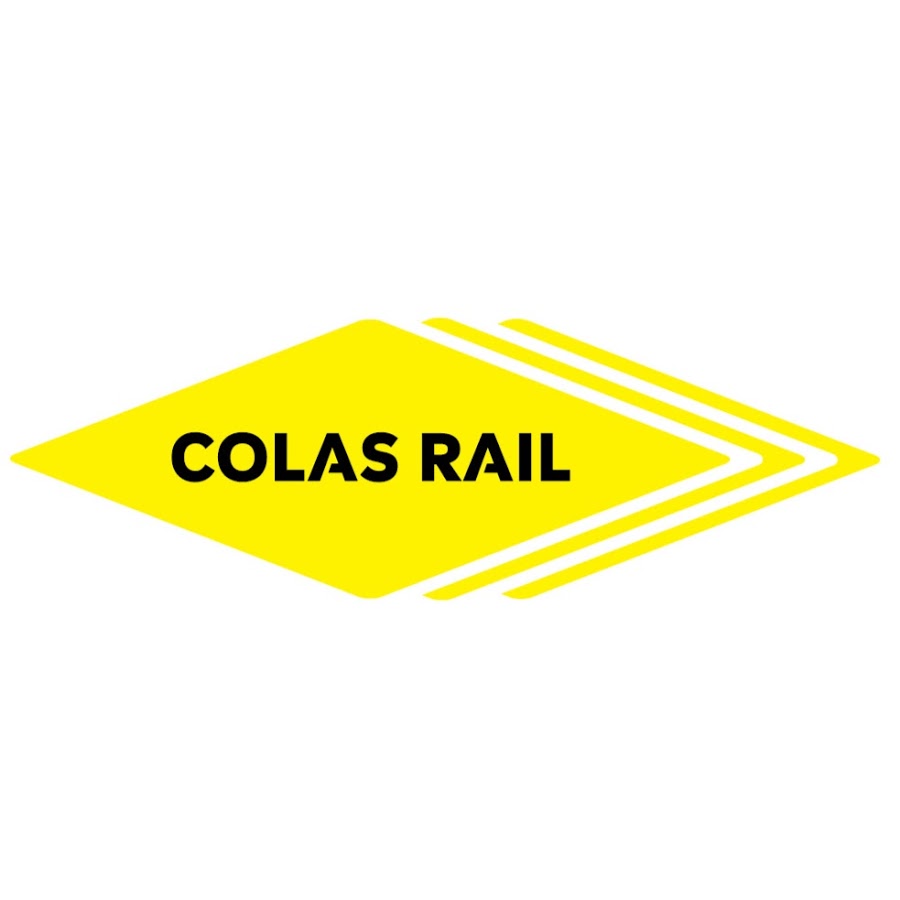
Key Points
- AECOM engineers needed a monitoring scheme to verify findings of their structural assessment and ensure safety during construction works
- Wireless monitoring solutions ensured a continuous data transfer in challenging site conditions
- Sensors on the tunnel lining allowed the anticipated movements to be monitored without interfering with the works